Level measurement is the process of determining the position of material – either liquid or solid – within a container, tank, silo, or other vessel. It is crucial in many applications for maintaining process efficiency, ensuring safety, and supporting inventory management, and is relied on in industries ranging from water treatment and food processing to oil and gas and chemical manufacturing.
Integral to this process are level measurement sensors, of which there are two main categories of technologies: point level measurement and continuous level measurement.
Types of Level Measurement
Point Level Measurement
Point level measurement refers to the detection of whether the level of a material (typically liquid, powder, or granular solids) in a container has reached a specific, pre-set point. These sensors are typically used to indicate conditions like "full," "empty," or a designated alarm level, triggering a control response or alert when that level is reached.
Common Types
- Float Switches
- How They Work: A float rises or falls with the material, mechanically triggering a switch
- Best For: Clean, non-viscous liquids
- Conductive Sensors
- How They Work: Use electrodes to detect conductive liquids
- Best For: Water-based liquids
- Vibrating Sensors
- How They Work: A vibrating fork changes frequency or stops vibrating when covered by material
- Best For: Powders and fine solids
Key Applications
- Overflow Protection – Alerting when a tank is full
- Pump Control – Turning pumps on/off at low/high levels
- Safety & Compliance – Ensuring hazardous materials stay within safe levels
Continuous Level Measurement
Continuous level measurement is a method used to monitor the exact level of a material (such as a liquid, slurry, or bulk solid) within a tank, silo, or vessel over the entire height of the container. Instead of detecting just one point, this type of measurement provides real-time, uninterrupted data on how much material is present, often expressed as a percentage, volume, or height.
- Ultrasonic Level Sensors
- How They Work: Emit sound waves that reflect off the material surface - the time it takes to return determines level
- Best For: Liquids and solids in open or closed tanks
- Radar Sensors
- How They Work: Send high-frequency radar signals that reflect off the material - the return time indicates level
- Best For: Harsh environments, steam, or high-pressure tanks
- Hydrostatic Sensors
- How They Work: Measure the pressure exerted by the material at the bottom of the tank to calculate level
- Best For: Liquid applications with known densities
Key Applications
- Inventory Management – Monitoring tank levels to optimize storage and refilling schedules.
- Process Control – Ensuring consistent material flow in manufacturing or mixing processes.
- Safety Systems – Preventing overfill or depletion of critical materials.
- Batching & Dosing – Accurately measuring amounts for repeatable production.
Choosing the Right Level Measurement Technology
When selecting a level measurement solution, it's essential to understand the difference between contact and non-contact sensors. Each has its advantages depending on the material type, environmental factors, and maintenance needs.
Contact Level Sensors
Contact level sensors are devices that physically touch the material they’re measuring, making them ideal for clean, stable liquids or solids that don’t pose excessive wear on the sensor. Common types include float switches, conductive probes, and hydrostatic pressure sensors. These technologies are often chosen for their simplicity and effectiveness in straightforward applications like monitoring water or fuel levels.
One of the main advantages of contact sensors is their cost-effectiveness, as they typically require a lower initial investment. They also offer high accuracy in the right conditions and are well-suited for less complex systems due to their simple design. However, because they’re in direct contact with the media, these sensors may require more frequent maintenance. They can wear out faster and may struggle with materials that are corrosive, sticky, or prone to buildup, all of which can impact long-term performance.
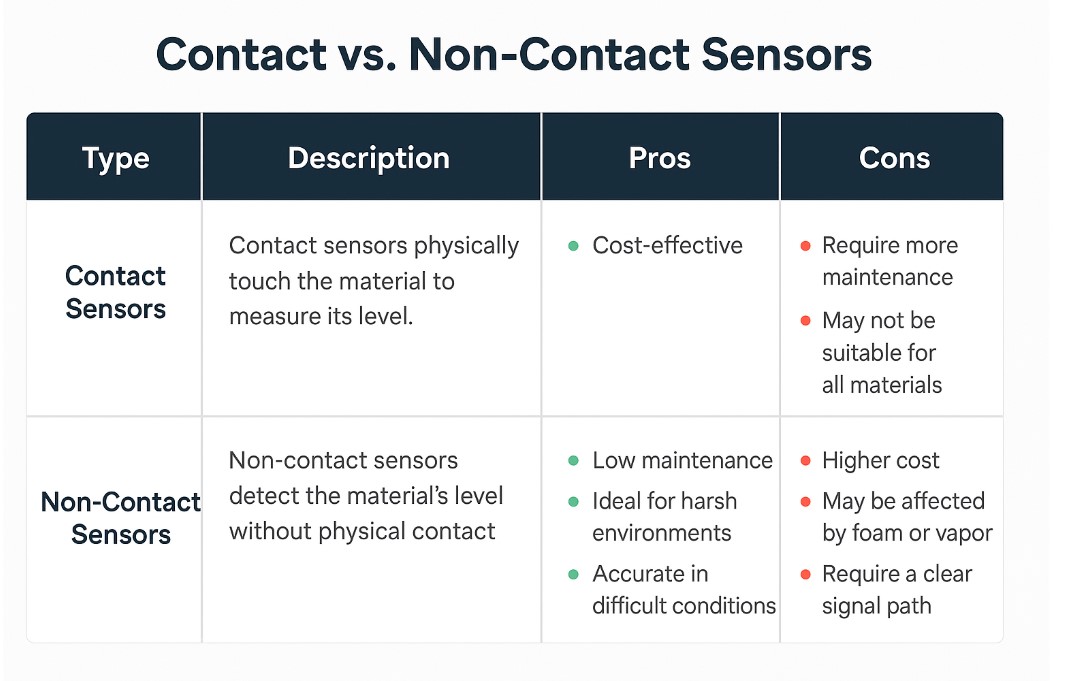
Non-Contact Level Sensors
Non-contact level sensors measure material levels without making physical contact, relying instead on technologies like ultrasonic waves, radar, or laser signals. This makes them an excellent choice for challenging applications—especially those involving corrosive, sticky, or high-temperature materials—and environments where cleanliness or safety is a priority. Their design allows for accurate readings even in sealed or pressurized tanks, with minimal need for maintenance.
The key advantage of non-contact sensors is their durability and low upkeep, as the lack of direct material exposure significantly reduces wear. They are particularly well-suited for harsh or hygienic conditions where traditional contact sensors may struggle. However, this performance comes at a higher cost, and their accuracy can sometimes be compromised by obstructions like foam, dust, or vapor. Additionally, these sensors require an unobstructed signal path to function properly, which can be a limitation in cluttered or complex tank setups.
Applications Across Industries
Water & Wastewater Treatment
Level measurement plays a critical role in water and wastewater management, from monitoring water levels in tanks and reservoirs to detecting sludge or foam buildup in clarifiers. Reliable level sensing also ensures efficient pump station control and helps prevent costly overflows—making it essential for maintaining safe, compliant, and efficient operations.
The Series PBLT2 Submersible Level Transmitter is designed for use in the harsh conditions typical of water and wastewater treatment. It uses a piezoresistive sensing element housed in a 316 stainless steel body to measure the height of liquid relative to atmospheric pressure. Its robust design includes a large, non-clogging stainless steel diaphragm seal that protects the sensor from damage caused by suspended solids, making it ideal for applications involving sludge, slurry, and other challenging media commonly found in water and wastewater systems. The PBLT2 also includes dual arrestor lightning and surge protection grounded to the case, helping to minimize the effects of power surges and ground strike transients in exposed or outdoor installations.
HVAC
In HVAC systems, precise level measurement is crucial for maintaining system efficiency and reliability. It helps monitor condensate levels in drain pans and pump reservoirs, detect overflow in humidifiers and air handling units, and manage refrigerant or glycol levels in chiller systems. Additionally, level monitoring ensures proper fuel levels in backup heating systems, such as oil tanks, to prevent disruptions during critical times. These measurements contribute to smoother operations, energy savings, and reduced risk of system failure.
The Series WD3 Water Leak Detector is designed to help prevent water damage in HVAC systems by detecting leaks in areas such as drip pans under air handler units. Depending on the model, it can provide audible and visual alerts, as well as a switch output for remote notification or control. For locations without access to power, a battery-powered version is available, while other models can operate on either AC or DC voltage. The sensing height is adjustable down to 1/32" using the included mounting bracket, which can be installed with adhesive strips or screws on flat surfaces.
Food & Beverage
In the Food & Beverage industry, precise level measurement ensures the smooth operation of critical processes. It enables effective level control in storage tanks for ingredients such as milk, syrup, and oils, and helps prevent overflow in mixing and blending tanks. Level sensors also play a key role in CIP (clean-in-place) systems, ensuring sanitation standards are met by accurately monitoring fluid levels during cleaning cycles. This level of control enhances product quality, safety, and efficiency throughout the production process.
The Series OLS Optical Level Switch provides a simple and reliable way to detect liquid levels in food and beverage processing systems. It uses infrared light and a prism to determine whether liquid is present, without any moving parts that could wear out or contaminate the process. When the prism is in air, the light is reflected back to a sensor; when liquid covers the prism, the light is refracted into the liquid and not detected. This change is used to indicate the presence or absence of liquid. The switch includes red and green LEDs for clear local indication and is available in materials such as 316 stainless steel, polysulfone, and PFA to suit different process needs. Its small size and ability to mount either horizontally or vertically make it adaptable to various installation setups.
Oil & Gas
In the Oil & Gas industry, accurate level measurement is vital for ensuring operational efficiency and safety. It plays a crucial role in tank gauging at refineries and terminals, allowing for precise inventory management. Level sensors also monitor separators and wellhead storage, ensuring proper fluid separation and storage conditions. Additionally, these measurements are essential for leak detection in pipelines, helping prevent environmental hazards and costly disruptions. Effective level management is key to maintaining safe, compliant, and efficient operations across the sector.
The Series L4 Flotect® Explosion-Proof Float Switch is used to monitor liquid levels in tanks and is a practical option for oil and gas applications. It can control equipment such as pumps or valves or activate alarms based on the liquid level. The switch works through a simple magnetic mechanism: as the float rises or falls with the liquid, it moves a magnet that triggers an internal snap switch. This design avoids the use of bellows, springs, or seals, which are common failure points in harsh environments. The float arm is also designed to prevent it from getting stuck in a vertical position, improving reliability in typical oil and gas setups.
Pharmaceutical
In the pharmaceutical industry, precise level measurement is essential for maintaining product consistency and safety. It helps manage accurate fluid levels in reactors and fermenters, ensuring optimal conditions for chemical reactions and fermentation processes. Additionally, level sensors are crucial for ensuring proper levels in sterile systems and during batch mixing, helping maintain strict quality control and meet regulatory standards. These measurements contribute to reliable, efficient, and compliant production processes in the pharmaceutical sector.
The Series CLS2 Capacitive Level Switch is a practical option for level detection in pharmaceutical settings, where both precision and material compatibility are important. It works with liquids, powders, and bulk materials, making it suitable for various stages of pharmaceutical processing. The switch uses capacitive sensing technology to detect material levels without needing moving parts, which helps reduce maintenance. Wetted parts made from PVDF and 316 stainless steel are compatible with common cleaning and sterilization procedures. The weatherproof enclosure and DPDT output allow for flexible installation and integration, and a range of process connection options makes it adaptable to different system setups.
Chemical & Petrochemical
In the chemical and petrochemical industries, accurate level measurement is crucial for handling hazardous materials safely and efficiently. It ensures proper monitoring of caustic or hazardous chemicals in pressurized tanks, reducing the risk of accidents. Level sensors also detect critical levels in solvent storage, preventing spills and ensuring safe containment. Additionally, interface detection, such as oil/water separation, is vital for maintaining product quality and preventing contamination. These measurements help optimize safety, compliance, and operational efficiency in high-risk environments.
The Series F6 & F7 Horizontal Float Level Switches are designed for use in demanding environments - like chemical and petrochemical applications, where accurate level monitoring is essential. These switches can be mounted through the walls of tanks or vessels, with options for both internal and external installation depending on the setup. They are suitable for a wide range of applications, including monitoring viscous liquids, detecting low levels, and even providing non-intrusive external mounting options when needed. Additionally, some models are ideal for leak detection in sumps or standpipes and can be used for groundwater monitoring. These switches offer flexibility and reliability in challenging industrial environments.
Contact a DwyerOmega Expert Today!