An Electromagnetic flow meter, also known as a magnetic flow meter or a magmeter, is a type of flow meter that is used to determine the flow of liquid in a pipe. These devices operate pursuant to Faraday’s Law of Electromagnetic Induction – which states that a voltage will be induced when a conductor moves through a magnetic field.
In an electromagnetic flow meter, a magnetic field is generated and channeled into the liquid flowing through the pipe, causing a voltage signal to be sensed by electrodes located on the flow tube walls. Faraday’s Law states that the voltage generated is proportional to the movement of the flowing liquid. When the fluid moves faster, more voltage is generated.
In contrast with many other flow meter technologies, electromagnetic flow meters produce signals that are linear with flow. As such, the turndown associated with magnetic flow meters can approach 20:1 or better – without sacrificing accuracy.
How Do Electromagnetic Flow Meters Work?
Electromagnetic flow meters, which are most commonly installed into pipes, consist of a tube with coils that generate a magnetic field and electrodes that detect voltage induced by the moving fluid. As a conductive fluid flows through a pipe of diameter (D) and through a magnetic field density (B) generated by the coils, the amount of voltage (E) developed across the electrodes – as predicted by Faraday’s Law – will be proportional to the velocity (V) of the liquid. Because the magnetic field density and the pipe diameter are fixed values, they can be combined into a calibration factor (K), and the equation reduces to:
E = KV
The velocity differences at different points of the flow profile are compensated for by a signal-weighing factor. Compensation is also provided by shaping the magnetic coils such that the magnetic flux will be greatest where the signal weighing factor is lowest.
Manufactures determine each magmeter’s K factor by water calibration of each flow tube. The K value thus obtained is valid for any other conductive liquid and is linear over the entire flow meter range. For this reason, flow tubes are usually calibrated at only one velocity. Magmeters can measure flow in both directions, as reversing direction will change the polarity but not the magnitude of the signal.
The K value obtained by water testing might not be valid for non-Newtonian fluids (with velocity-dependent viscosity) or magnetic slurries (those containing magnetic particles). These types of fluids can affect the density of the magnetic field in the tube. In-line calibration and special compensating designs should be considered for both of these fluids.
Common Applications for Electromagnetic Flow Meters
Electromagnetic flow meters can detect the flow of clean, multi-phase, dirty, corrosive, erosive, or viscous liquids and slurries as long as their conductivity exceeds the minimum required for the particular design. These devices are widely used across various industries due to their accuracy, reliability, and ability to measure the flow of conductive liquids without any moving parts.
Some key applications include:
- Water and Wastewater Treatment
- Electromagnetic flow meters excel in handling clean water, raw sewage, sludge, and chemicals used in treatment processes.
- They offer high accuracy and no pressure drop, which is essential for large-scale municipal water management.
- Since they have no moving parts, they are highly resistant to debris and solid particles present in wastewater.
- Chemical Processing
- Magmeters can measure aggressive and corrosive liquids – like acids, alkalis, and other chemical solutions without being damaged.
- They are available with corrosion-resistant linear materials (e.g., PTFE, PFA) to withstand harsh chemicals.
- No obstruction in the flow path means they do not get clogged or affected by sedimentation.
- Food and Beverage Industry
- Used for measuring milk, beer, juices, syrups, and other food-grade liquids that require hygienic conditions.
- Magmeters can be designed with sanitary fittings (e.g., stainless steel) to met FDA and EHEDG standards.
- Their non-intrusive design ensures there is no contamination or disruption in the production process.
- Pulp and Paper Industry
- Capable of handling high-viscosity and fiber-laden fluids – such as pulp slurries and coating solutions.
- No moving parts means minimal wear and tear – even when dealing with abrasive slurry.
- Provides consistent measurement despite fluctuations in fluid density and composition.
- Mining and Mineral Processing
- Used for measuring the flow of mineral slurries and abrasive fluids in extraction refining operations.
- Their rugged construction allows them to withstand harsh environmental conditions.
- No mechanical wear from abrasive particles ensures long-term reliability and low maintenance.
- Power Generation (Cooling Water and Boiler Feedwater)
- Commonly used in thermal and nuclear power plants for monitoring cooling water and feedwater flow rates.
- They can handle large pipe sizes and provide highly accurate measurement for flow monitoring and efficiency calculations.
- No moving parts means they can operate in high-temperature environments with minimal maintenance.
- Pharmaceutical and Biotechnology
- Used for measuring the flow of purified water, solvents, and active pharmaceutical ingredients with high precision.
- Electromagnetic meters with sterile designs and CIP/SIP (clean-in-place/steam-in-place) compatibility are ideal for pharmaceutical applications.
- Non-contact measurement ensures sterility and compliance with industry regulations.
- Agriculture and Irrigation Systems
- Ideal for monitoring the flow of water, fertilizers, and pesticide solutions in irrigation systems.
- Can operate in low-pressure systems without causing significant pressure loss.
- Their long lifespan and minimal maintenance make them cost-effective for agricultural use.
- Oil and Gas (Produced Water and Brine Injection)
- Used for monitoring produced water, brine injection, and chemical dosing in upstream and downstream operations.
- Their ability to measure conductive fluids with high accuracy makes them ideal for these applications.
- Explosion-proof and hazardous area-rated designs ensure safe operation in oilfield environments.
- Steel and Metal Industry
- Used for monitoring the flow of cooling water in continuous casting and rolling mill operations.
- Provides accurate flow readings in high-temperature environments without mechanical failure.
- Can handle scale-laden water without clogging or performance degradation.
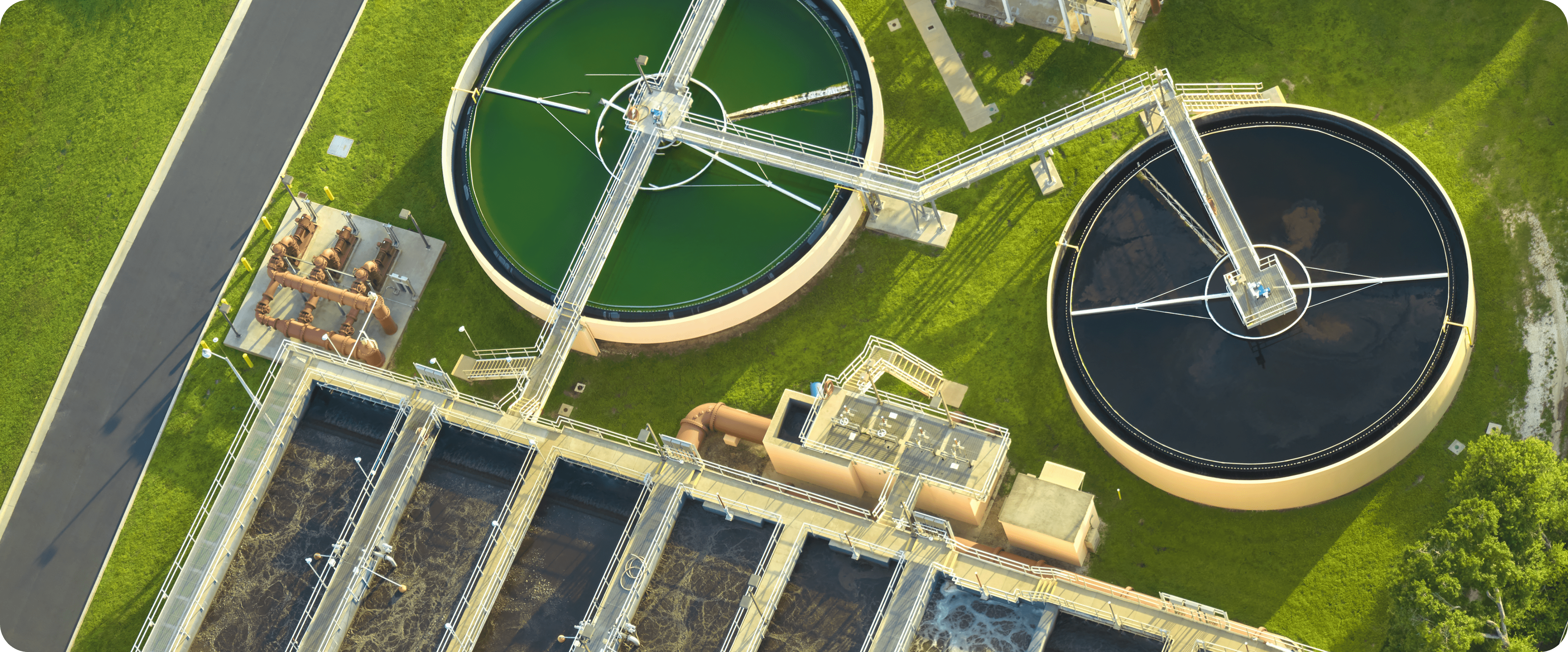
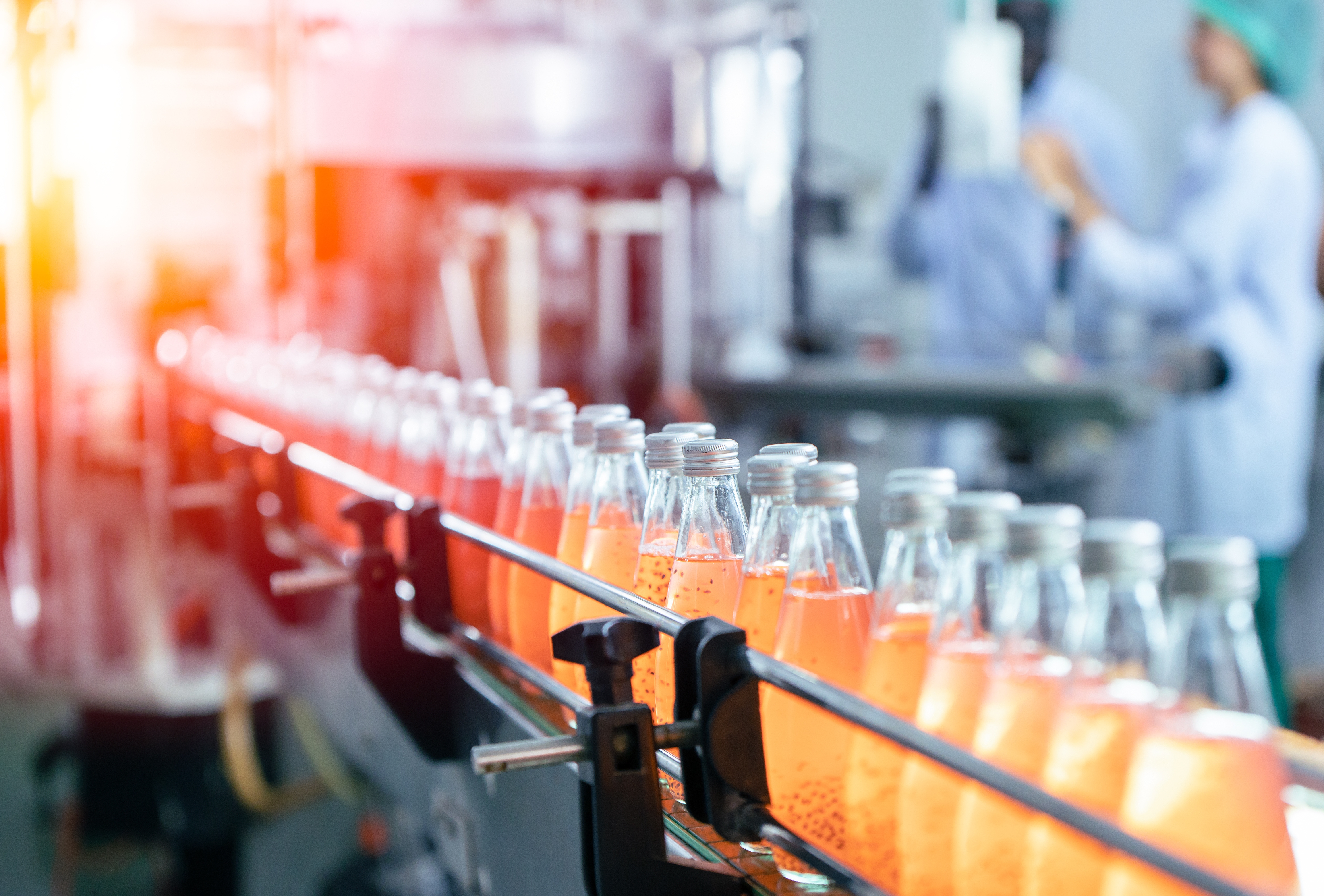
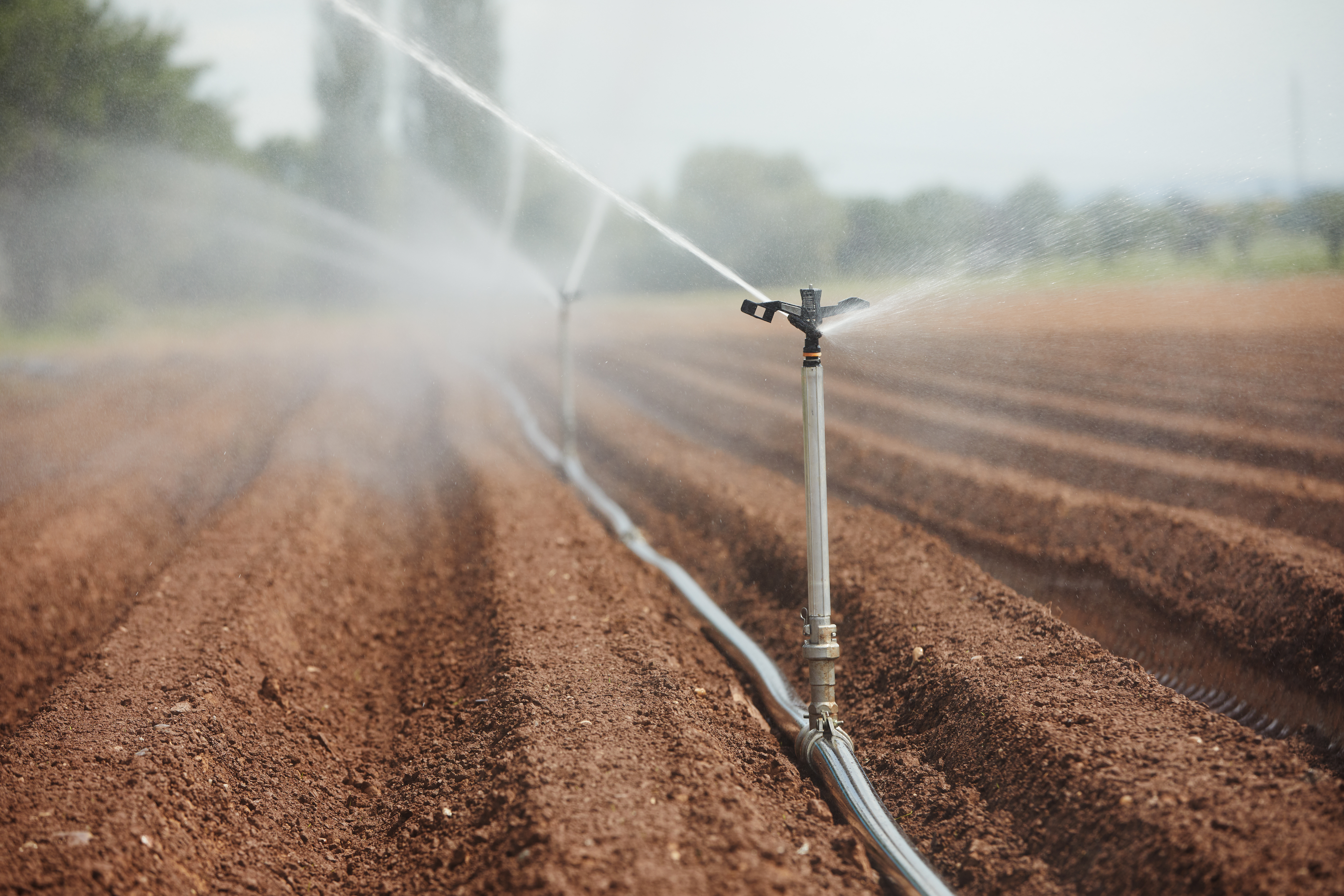
Application Cautions for Magnetic Flow Meters
Do not operate a magnetic flow meter near its electrical conductivity limit because the flow meter can turn off. Provide an allowance for changing composition and operating conditions that can change the electrical conductivity of the liquid.
In typical applications, magnetic flow meters are sized so that the velocity at maximum flow is approximately 2-3 meters per second. Differential pressure constraints and/or process conditions may preclude application of this general guideline. For example, gravity fed pipes may require a larger magnetic flow meter to reduce the pressure drop so as to allow the required amount of liquid to pass through the magnetic flow meter without backing up the piping system. In this application, operating at the same flow rate in the larger flow meter will result in a lower liquid velocity as compared to the smaller flowmeter.
For slurry service, be sure to size magnetic flow meters to operate above the velocity at which solids settle (typically 1 ft/sec), in order to avoid filling the pipe with solids that can affect the measurement and potentially stop flow. Magnetic flow meters for abrasive service are usually sized to operate at low velocity (typically below 3 ft/sec) to reduce wear. In abrasive slurry service, the flow meter should be operated above the velocity at which solids will settle, despite increased wear. These issues may change the range of the flow meter, so its size may be different than the size for an equivalent flow of clean water.
Contact Us Today!