The Challenge
- Design a ventilator that meets regulatory requirements
- Easy to manufacture from low-cost components
- Uses generic parts that are easy to source
Solution
- OMEGA PXM 309 Series industrial pressure transducers
- OMEGATXDIN 1620 DIN Rail Transmitter
Results
- Robust ICU-ready ventilator design
- No specialist or medical supply chain components required
- Low-cost, quick and easy to manufacture and maintain
The Challenge
The COVID-19 pandemic has created worldwide demand for ventilators—with approximately 880,000 more needed. Existing ventilator manufacturers are struggling to produce enough ventilators to meet the demand, primarily due to disruptions in the supply chain and a dwindling inventory of specialized components.
To try and fill the gap, the United Kingdom's (UK) Medicines and Healthcare products Regulatory Agency Department of Health and Social Care (MHRA) issued specifications for developing a "minimally acceptable," rapidly manufactured ventilator system.
Taking up the challenge, was a team of multidisciplinary experts at the Imperial College of London, including Dr. Joseph Sherwood, an RAEng Research Fellow at the Department of Bioengineering, along with his co-technical lead Dr. Michael Madekurozwa, Department of Bioengineering, Professor James Moore, the Bagrit Chair in Medical Device Design, and Dr. Jakob Mathiszig-Lee, Honorary Research Fellow and Senior Anaesthetic Registrar at the Royal Brompton Hospital.
However, they wanted to do more than design a viable ventilator – they wanted to build one that would address the fundamental, underlying issues around the ventilator shortage.
"The main reason why the ventilator challenge started in the first place is because the big ventilator manufacturers didn't have enough parts," said Dr. Sherwood. "Most existing designs involve complex, proportional control valves and flow sensors, and there just aren't enough in stock."
Dr. Sherwood noted that most ventilators are designed to function with proportional control valves from a single supplier. "That's the crux of it, you just can't get a high number of those valves," he said. "Our take was to provide the same functionality that the ICU ventilators provide, but find alternative components that wouldn't drain the ventilator supply chain."
The team also had the ambitious goal to design a ventilator that would be low cost, viable for long-term use beyond the crisis, and quickly and easily manufactured in different parts of the world. If they could achieve these goals, they would be able to help countries with limited budgets and resources gain more access to much-needed ventilators.
The Solution
The ventilator Dr. Sherwood and his team designed, known as JAMVENT, uses standard products only – nothing is custom designed. And many of these products, such as the OMEGA PXM 319 series industrial pressure transducers and the OMEGA TXDIN 1620 DIN Rail Transmitter, were components that Dr. Sherwood had lying around his lab and was using for other research projects.
"We didn't have the time to place orders and wait for delivery, so we just played with what we had," said Dr. Sherwood, who noted they put a working prototype together within three days.
The critical components in the design of the ventilator are the valves, which are simple on-off solenoid valves that are provided by a large range of different manufacturers, instead of complex proportional valves used in other ventilator designs. Two of the valves control the mixing of air and oxygen in a two-liter reservoir, while the pressure is monitored by an PXM 319 series pressure transducer. The inhalation valve then opens to deliver the breath to the patient, with the pressure downstream monitored by a second PXM319.
"The pressure drop across the valve is very predictable based on fluid dynamics principles, so we can calculate very precisely the flow rate moving from the reservoir to the patient," said Dr. Sherwood. "This avoids the need to purchase flow meters, which are also in short supply."
The oxygen concentration of the delivered breath is monitored with an oxygen sensor, and an Omega TXDIN 1620 is used to amplify the signal cleanly. The exhalation valve has a low resistance to flow, enabling rapid exhalation, which is very important when the resistance of the lungs is high, such as in COVID-19 patients.
The ventilator system is designed to provide the clinician-selected volume for each breath while minimizing the pressure in the lung. It operates in Pressure Regulated Volume Control (PRVC) mode and has additional modes that can support spontaneous breathing and maintenance of PEEP during suction.
Additionally, the design does not use Bag Valve Masks, which are the basis for most emergency ventilators, but the team determined could be hard to source and may lack longevity. Instead, they switched to a two-liter bottle, which gave them enough compressible gas volume to get the functionality they needed.
The flexibility of the design means that it can operate on hospital gas supply lines or with the lower pressures generated by oxygen concentrators. This was an important feature for meeting the goal of making the ventilator more accessible to parts of the world with limited resources, which can often include a lack of access to gas supply infrastructure.
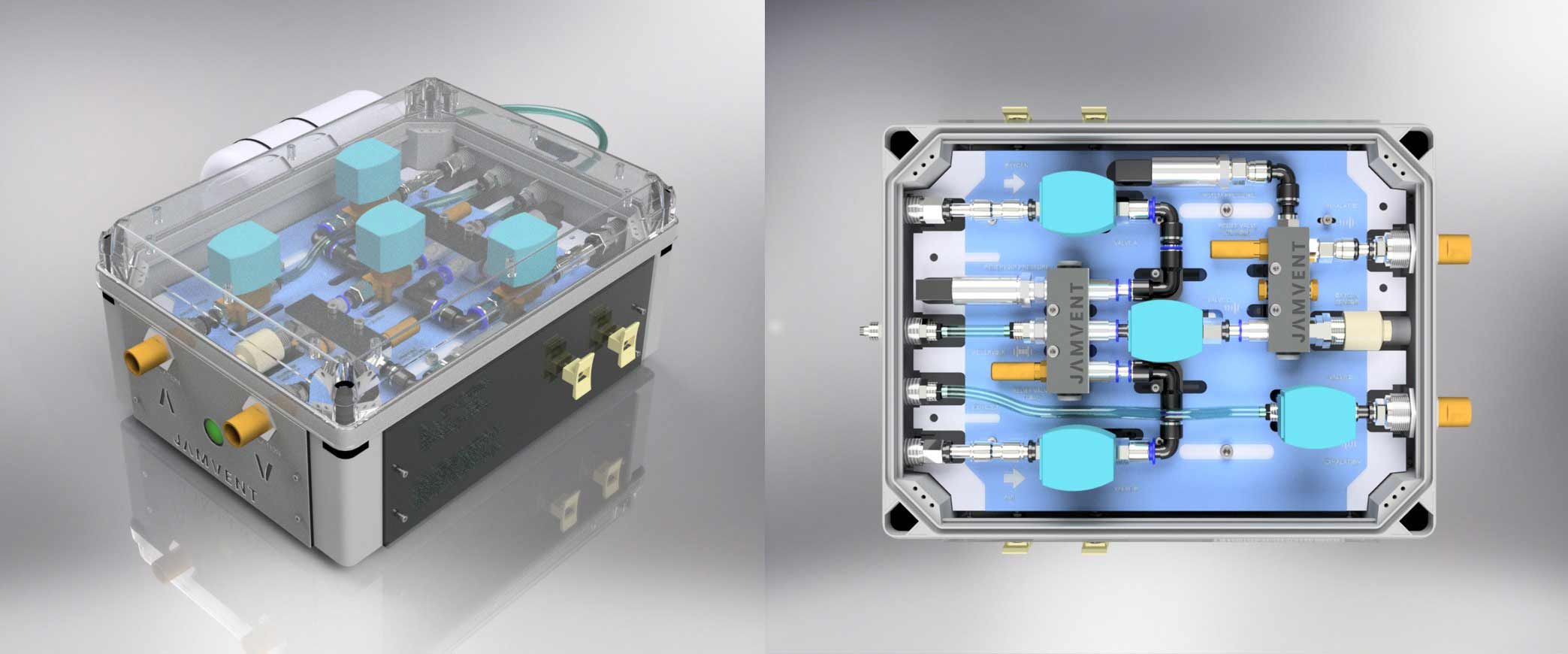
The Results
Most medical devices take five years to bring to market and cost somewhere between $30 million to $100 million. However, a working prototype of JAMVENT was developed on a meager budget of $55,000, plus the incalculable value of the time volunteered by the many people involved in the project. And, within one month, the team demonstrated the performance required by the MHRA RMVS scheme. Plans are underway with multiple industrial partners for large-scale manufacturing of the device.
The design of the JAMVENT is not only groundbreaking in its affordability and flexibility, but it also meets all of the team's original goals, including:
- Robust design suitable for long-term use
- Meets all capabilities needed for an ICU ventilator
- Easy and low-cost to manufacture (estimate component cost is $1,900/£1,500)
- Doesn't require any specialist or medical supply chain components
- Parts are standard and available from various manufacturers
- Simple electronics for easy manufacturing and maintenance
- Open, modular design that provides greater flexibility for local manufacturing
"In a sense, it was quite an innovative way of thinking about the problem because it wasn't just that we wanted to create an emergency ventilator, we wanted to design something that wouldn't add any stress to the existing manufacturers or supply chains," said Dr. Sherwood.
More than just innovative, the JAMVENT, is being described by Forbes as a "frugal engineering marvel" and "potentially game-changing business model innovation in the medical device market" that "has the potential to disrupt the market by demonstrating a superior approach."