To measure strain using a bonded resistance strain gauge, the gauge must be part of an electrical circuit capable of detecting small resistance changes. A Wheatstone bridge is a fundamental circuit used for this purpose, enabling precise measurement of minute resistance variations by balancing two voltage dividers. When the circuit is in equilibrium, the output voltage is zero, but when strain causes a change in resistance, an imbalance occurs, generating a measurable voltage signal. This makes the Wheatstone bridge highly effective for strain measurement, as it enhances sensitivity and compensates for potential error sources like temperature fluctuations.
What is a Wheatstone Bridge?
A Wheatstone bridge is an electrical circuit designed to precisely measure unknown resistances by balancing two voltage divider networks – commonly referred to as “legs” – of the bridge. The circuit operates on the principle of null deflection, meaning when the bridge is balanced, no current flows through the detection instrument.
Circuit Configuration
The Wheatstone bridge consists of:
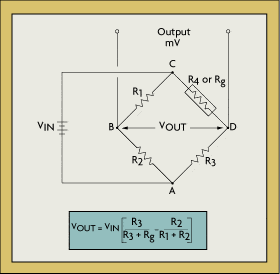
- Four resistors arranged in a diamond (bridge) shape:
- Two known resistances (R1 and R2)
- One adjustable resistance (R3 – a variable resistor)
- One unknown resistance to be measured (R4 or Rg)
- A DC voltage source (VIN) applied across opposite corners of the bridge (between points A and C)
- A galvanometer (or voltmeter) connected across the middle points (B and D)
How Does a Wheatstone Bridge Work?
The accuracy of a Wheatstone bridge relies on whether the bridge is balanced or unbalanced. Understanding these conditions is key to how the circuit detects and measures an unknown resistance.
A balanced Wheatstone bridge occurs when the ratio of resistances in one leg of the bridge equals the ratio in the other leg. In this state, the voltage at both midpoints of the circuit is the same, meaning no current flows through the galvanometer (the measuring device). When the bridge is balanced, the unknown resistance can be determined using a simple equation without interference from external factors, making this an ideal method for precise measurements.
An unbalanced Wheatstone bridge happens when the resistance ratios do not match, causing a voltage difference between the midpoints. This imbalance results in a current flowing through the galvanometer, creating a measurable deflection. The direction and magnitude of this deflection indicate the difference between the expected and actual resistance values. By adjusting one of the known resistances or analyzing the voltage difference, the unknown resistance can be accurately determined. This unbalanced state is useful in sensor applications, such as strain gauges or temperature sensors, where small resistance changes need to be continuously monitored.
The Chevron Bridge Circuit
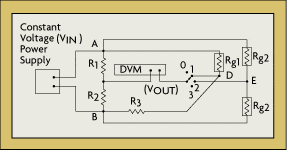
The Chevron Bridge is a multiple channel arrangement that serves to compensate for the changes in bridge-arm resistances by periodically switching them. Here, the four channel positions are used to switch the digital voltemeter (DVM) between G-bridge (one active gauge) and H-bridge (two active gauges) configurations. The DVM measurement device always shares the power supply and an internal H-bridge. This arrangement is most popular for strain measurements on rotating machines, where it can reduce the number of slip rings required.
Why Strain Gauges Need Wheatstone Bridge Circuits
A strain gauge is a sensor that measures mechanical deformation by converting strain (stretching or compression) into a change in electrical resistance. However, this resistance change is typically very small, making it difficult to measure directly with high precision. This is where the Wheatstone bridge plays a crucial role.
By using different Wheatstone bridge configurations — quarter bridge (one strain gauge), half bridge (two strain gauges), or full bridge (four strain gauges) — the sensitivity and accuracy of the measurement can be enhanced. Additionally, a full-bridge setup can help compensate for temperature variations and other external factors that might affect resistance. This combination of strain gauges and Wheatstone bridge circuits is widely used in industrial applications such as load cells, pressure sensors, and structural health monitoring systems.
Strategic Installation
Strain gauge circuits produce low-level voltage signals, often requiring sensitivities around 100 microvolts or better. This makes them particularly susceptible to noise from electrical devices. Potential error sources include capacitive coupling from lead wires running near AC power cables, magnetic induction from variable magnetic fields, parasitic contact resistances in lead wires, insulation failures, and thermoelectric effects at junctions of dissimilar metals. These interferences can significantly degrade signal quality.
Shielding
To mitigate electrical interference and noise, implementing proper shielding is crucial. Enclosing measurement lead wires within a shield intercepts external interferences and can reduce errors from insulation degradation. Shielding also protects against capacitive coupling. When measurement leads are routed near sources of electromagnetic interference, such as transformers, twisting the leads helps minimize signal degradation due to magnetic induction by canceling out induced currents. In industrial applications, twisted and shielded lead wires are commonly employed to maintain signal integrity.
Guarding
Beyond shielding, guarding the instrumentation itself is equally important. A guard, typically a sheet-metal enclosure surrounding the analog circuitry, is connected to the shield to ensure all components are at the same electrical potential, preventing extraneous current flows. Ground currents flowing through the strain gauge element or its lead wires can be indistinguishable from the measurement signal in a Wheatstone bridge circuit. Implementing guarding ensures that terminals of electrical components remain at the same potential, thereby preventing error-inducing currents. Additionally, connecting a guard lead between the test specimen and the negative terminal of the power supply provides an alternative path for error-producing currents, ensuring all elements involved are at the same potential as the test specimen.
Lead-Wire Effects
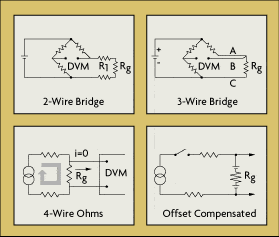
Strain gauges are sometimes mounted at a distance from the measuring equipment. This increases the possibility of errors due to temperature variations, lead desensitization, and lead-wire resistance changes. In a two-wire installation, the two leads are in series with the strain-gauge element, and any change in the lead-wire resistance (R1) will be indistinguishable from changes in the resistance of the strain gauge (Rg).
To correct for lead-wire effects, an additional, third lead can be introduced to the top arm of the bridge. In this configuration, wire C acts as a sense lead with no current flowing in it, and wires A and B are in opposite legs of the bridge. This is the minimum acceptable method of wiring strain gauges to a bridge to cancel at least part of the effect of extension wire errors. Theoretically, if the lead wires to the sensor have the same nominal resistance, the same temperature coefficient, and are maintained at the same temperature, full compensation is obtained. In reality, wires are manufactured to a tolerance of about 10%, and three-wire installation does not completely eliminate two-wire errors, but it does reduce them by an order of magnitude. If further improvement is desired, four-wire and offset-compensated installations should be considered.
In two-wire installations, the error introduced by lead-wire resistance is a function of the resistance ratio R1/Rg. The lead error is usually not significant if the lead-wire resistance (R1) is small in comparison to the gauge resistance (Rg), but if the lead-wire resistance exceeds 0.1% of the nominal gauge resistance, this source of error becomes significant. Therefore, in industrial applications, lead-wire lengths should be minimized or eliminated by locating the transmitter directly at the sensor.
Temperature and the Gauge Factor
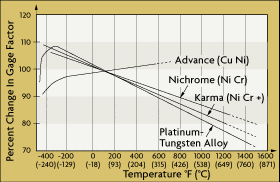
Strain-sensing materials, such as copper, change their internal structure at high temperatures. Temperature can alter not only the properties of a strain gauge element but also can alter the properties of the base material to which the strain gauge is attached. Differences in expansion coefficients between the gauge and base materials may cause dimensional changes in the sensor element. Therefore, a temperature compensation circuit would be needed.
Explore DwyerOmega's Complete Force & Strain Measurement Selection